Table of Content
Welcome to the world of worm farming, where you’ll not have one but 500 pet worms. By this time, the worms would have already migrated to the top bin leaving behind the finished compost that looks dark brown. However, it will take a while before the compost and worm castings are fully ready for the first harvesting.
A place for the discussion of all manner of metal casting and foundry work, whether in the backyard or on a commercial scale.
How to Design a Worm Gear System – What You Really Need to Know
All worm gears are made of two different metals, with a harder metal used for the worm and a softer one used for the wheel. This design enhances a worm gear‘s ability to absorb shock loads that are found in construction equipment and other applications that have heavy loads. One of the major benefits of worm gears is their ability to offer gear reduction and torque multiplication in a small footprint. The construction of a worm gear includes a large worm wheel that has a shallow thread and is connected to a perpendicular axes, non-intersecting gear. Stainless steel worm gears are made of 303 and 316 grade stainless steel. They are ideal for damp and wet conditions since they do not rust or corrode.
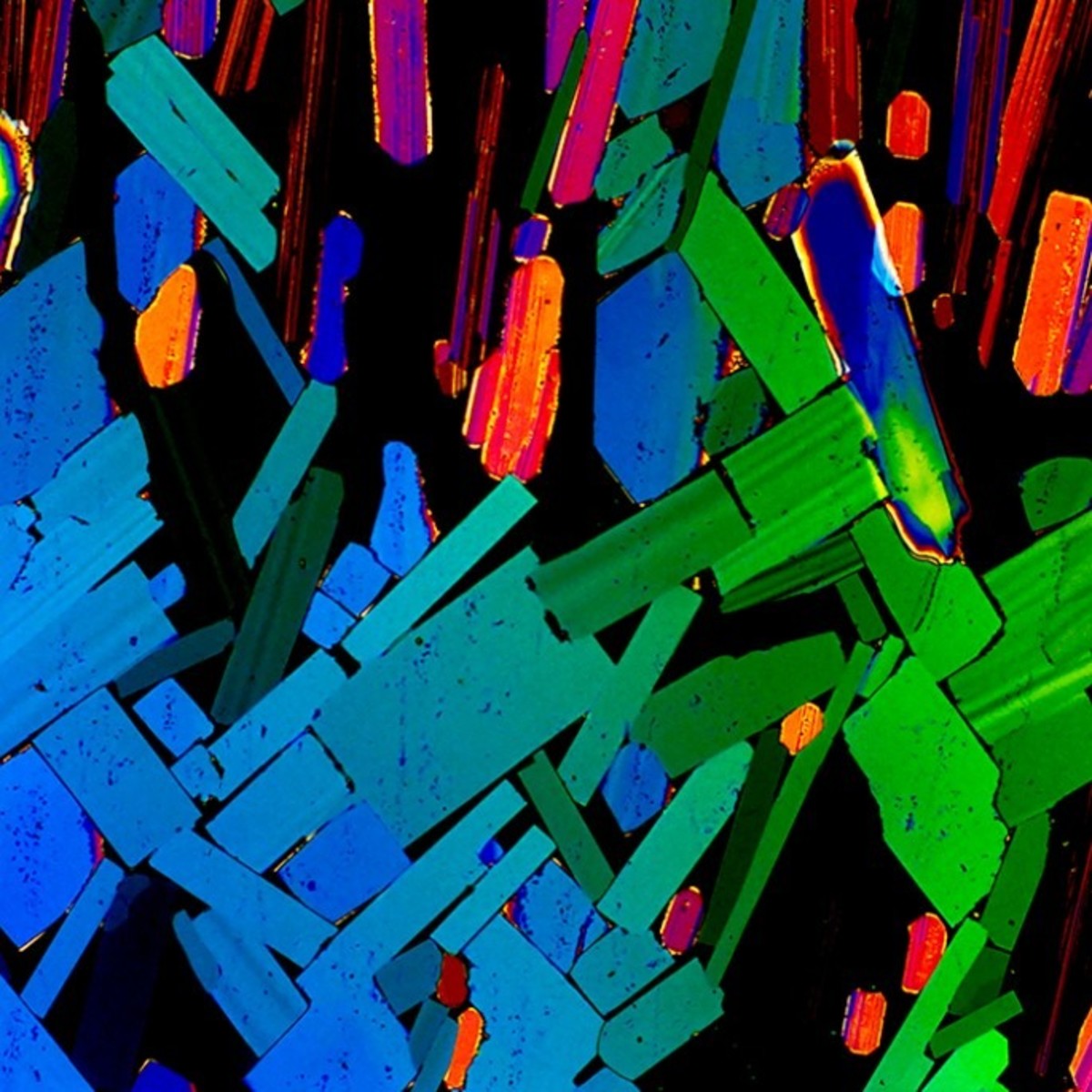
Worm farms are great for people with smaller gardens or no gardens as they take food scraps only. With worm farms, you’ll need to regularly feed your worms with food scraps, and they will in turn give you worm castings to use in the garden. The two basic types of worm gears are cylindrical or straight and cone or double enveloping. The faces of worm gears are broken into straight, hobbed, and concave. Apparently these Rockwells will “eat” that worm gear if you let the carriage get “too stiff” and use the power feeds much.
Lead Screw
If this is for a commercial product I suggest sourcing a readily available set that meets your needs. From experience, you will spend a lot of time and energy only to make something mediocre at best. And when it comes time for production you will probably need to outsource the gears. Doing it yourself will make you learn a lot but it may not be the best business solution. Janjigian explains that in a commercial oven there’s more room for the pizza, but in a backyard version, you have an intense heat source basically right next to the pie. That means there’s often more responsibility on you to rotate the pie once inside the oven to make sure it’s cooking evenly, around the circle, but also top and bottom.
The unique design of worm gears gives them the ability to stop quickly; this makes them the right choice for the operation of elevators. Though they can‘t make up the complete braking system, they work well with other braking system components as a safety measure. The precise mounting of a worm gear assembly is a critical part of its use. Several points of contact are required to avoid work loads over working the lead angle. The threaded wheels are made of an abrasive material that is harder than the metal to be ground.
Chapter Four - Uses for Worm Gears
In the milling process, the gear is cut in a milling or jig grinder using a gear cutter and indexing or rotary table. The teeth of the gear are created by a rotating multi-edge cutter that creates teeth that are similar to the cutter. The cutter moves axially along the length of the gear tooth at the correct depth. Once the teeth are cut, the cutter withdraws, and a new blank is indexed. Hobbing is a method for producing gear teeth using a set of customized bits that are designed to make the correct pitch for the gear‘s application.

They are normally used in conditions where cleanliness is a necessity such as food and beverage manufacturing. They are easy to clean and have smooth surfaces and exceptional durability. Much like bronze, brass is used to make the wheel gear; it is a softer metal and prevents wear on the shaft of the worm gear. The brass worm gear configuration is used for light loads since brass can only endure lower load amounts.
American Gear Manufacturer Association compounded oils classes 7 and 8 are normally used. Hobbing machines are fully automated and come in a wide variety of sizes to enable them to produce extremely small gears as well as large gears. The two parts of a hobbing machine include two spindles—one to hold the workpiece and one to hold the hob. This is the closest I have gotten to a completed curvy wormy by abusing the sweep tool but the teeth profiles on the worm are very inconsistent. I think I have just about given up on the sweep tool at this point and I am out of ideas how to fix this.
It is impossible for a lubricant to prevent gear wear indefinitely. A combination of natural and synthetic additives provide extra protection and increase the worm gear‘s longevity. In an automotive steering system, the worm gear connects to the steering wheel through the steering column. The turning of the steering wheel depends on the precise angle of the gear ratio of the worm gear system. Another aspect of worm gears in lifts or elevators is their non-reversibility, which serves as a failsafe braking system should the primary braking system fail. The tool that is used, the punch, is referred to as a hob and is made of hardened steel that forms a helical hob cutter.
I also seem to remember someone figured out (and posted on one of the boards?) how to single point a worm gear using a boring bar between centers. Any help (maybe links to worm wheel making in depth write-ups?) would be appreciated. Manganese bronze is very strong, there are a few bronze alloys stronger than mild steel.
Assembly with the Design Accelerator worm gear already inserted. You can put fruit and veggie scraps, but unlike compost bins, you need to exclude citrus and onions as worms don’t like them. Worm farms also take egg shells, cartons, newspaper, tea leaves and bread.